Masking can seem like a "simple" process that is often accomplished with masking tape slit to common widths and applied by hand to protect surfaces from paint, contamination, or damage. Similar to surface protection tapes, masking materials are often discarded long before the final product reaches the customer. So what benefits are seen by changing from rolls of tape to die-cuts specific for your application?
Custom Die-Cut Masking vs. Masking with Strips
One of our recent customers, a plastic injection molder of automotive body parts decided to see if die-cuts really would make a difference in their processes. , and take a look at the benefits they specifically saw when transitioning to die-cut masks below.
BENEFITS OF DIE-CUT MASKING:
- FASTER TAPE APPLICATION - In the time it previously took the customer to mask one part (68 seconds), workers could mask three parts
- 75% REDUCTION IN REWORK - Rework was drastically reduced as employees made fewer placement errors
- 60% REDUCTION IN LABOR COSTS - The company was able to reduce labor costs as a result from a faster, more efficient masking process
- REDUCED MATERIAL WASTE - Using die-cut components ensures the smallest material waste possible.
- REDUCED APPLICATION/REMOVAL TIME - With the addition of pull tabs, extended liners, and split liners, application and removal are simple.
- SAFER PROCESSES - Eliminates the need for applicators to use blades to hand trim strips of tape
*Other features added by die cutting: Tabs for easy assembly, liner to assist in handling, precise fit-to mask item, dry zones for quick release, and more...
Although a precision die-cut mask with a protective liner on the adhesive side is more expensive than the equivalent amount of tape on rolls, the improvements in process speed, rework, scrap and safety more than compensated for the increased material cost.”
-Paint Line Manager
Masking Solutions with Marian
Not only will Marian work closely with your engineers and design team to help design an effective solution for you, we will also ask questions to help guide you to the best top-of-the-line materials. As a converter on 3M's short list of preferred converters, we've developed strong relationships to make the highest performing


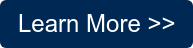
Do you like what you see and want to learn more? If you're interested in learning more about Marian and our wide variety of value-adding die cutting capabilities, contact us and one of our material specialists will reach out to you. We'd love to be the solution to your next application problem!